Progress tracking from engineering to the construction site
Customer project: Loesche GmbH
From production to the construction site, mechanical systems such as raw material mills or cement plants pass through many stages. Ordering processes in plant engineering are therefore often very complex and require cooperation between different departments. If the interlinking between production, purchasing, sales and project planning does not run smoothly, this can result in faulty deliveries, which can seriously delay construction projects. This can be counteracted with standardized, cross-departmental handling of all processes in SAP.
Intelligent add-ons expand the project management functions with important components and make working with a clear web interface easier. For over a year now, Loesche GmbH has also been supplementing the use of SAP across all departments with two additional tools from Milliarum for clear progress tracking of the ordering process and simplified project scheduling.
Loesche GmbH is an innovative, internationally oriented family business in the mechanical and plant engineering sector. The roller mill technology, patented back in 1928, has been continuously developed and has since become synonymous with the company. Creativity, dynamism and a willingness to innovate have made Loesche GmbH one of the world's leading suppliers of the best grinding technology. As an independent family-owned company with headquarters in Düsseldorf, we have a global presence with more than 850 employees, subsidiaries in the USA, Brazil, Spain, Germany, Great Britain, South Africa, India, the United Arab Emirates, Russia and China as well as representatives in more than 20 countries. In recent years, the company has been able to steadily expand its market position, which is not only reflected in rising sales and employee numbers, but also in a number of new major projects that need to be professionally coordinated.
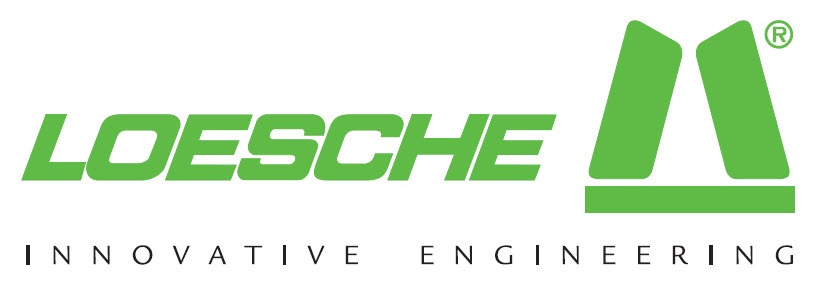
Complex projects require an integrated overall solution
Whereas just a few years ago, smaller projects could be handled without any problems using in-house IT solutions, Loesche's continuous growth made it necessary to look for a new integrative overall solution that would provide system support for large projects running in parallel. Previously, important project information was only partially managed via SAP, while other important project information was stored in local folder structures or the CAD management system. What was missing was an overview of the entire project. "We had reached a point where we realized that, due to the increasing complexity of the processes, we were no longer getting anywhere with isolated solutions in the individual departments, but that we needed a solution that integrates the upstream and downstream processes relating to an order," explains Annegret Dobelmann, Functional Area Manager for Service and Controlling in the Procurement department. The fact that the solution they were looking for had to work in harmony with the SAP standard was a decisive factor in the search for a suitable provider - after all, the aim was to prevent self-programmed individual solutions from separating the company from future SAP developments.
A suitable consulting and development partner was quickly found: Functional area manager Ulrich Fiebig, who is responsible for software organization at the company, came into contact with Dirk Ott at a specialist conference. He is the Managing Director of Milliarum GmbH, which specializes in solutions in the SAP environment for the optimization of business processes for the implementation of projects. "What we particularly appreciate about Milliarum as a consulting and development partner is that the staff are familiar with plant engineering and therefore speak our language, but at the same time are always two or three steps ahead of us mentally," says Ulrich Fiebig, explaining the quick decision to work with the SAP service provider.
Agile software development ensures employee acceptance
In the first quarter of 2011, the first step was to analyze the current situation in the company and hold various workshops to work out how the various procurement processes actually work, how they are perceived from the perspective of different departments such as purchasing or design and what difficulties arise in the process. Shortly afterwards, the second project phase was initiated, in which the workshops were accompanied by an SAP prototype and two standardized SAP add-ons for progress tracking and project scheduling. This allowed the processes to be carried out and tested directly in the prototype and further refined on this basis.
Milliarum SAP add-on: Project scheduling
The final implementation of the new solution and the SAP add-ons was continuously accompanied by an intensive training phase, whereby the individual training sessions were always held very close to the active use of the new SAP solution in the individual departments. This allowed users from the various departments to immediately implement the content taught on the system and in turn provide important feedback for the final fine-tuning. Thanks to this agile software development, it was possible to achieve a high level of acceptance of the new solution among users in the company, even though the changeover involved some serious changes. "After all, the conversion of our logistics was not just an IT project, but also a change process that also involved optimizing the structures behind our ordering processes," explains Ulrich Fiebig.
After initially handling ongoing projects in the old way for around six months, but already managing new ones using the newly developed solution, almost 125 users from departments such as Purchasing, Shipping, Design and Project Execution are now using the system at the Düsseldorf site. Users access the Milliarum Cockpit via the intranet with a user-friendly web interface and, thanks to intelligent progress tracking, can see at a glance what the overall order status is for individual projects. With just a few clicks, it is possible to filter out which partial orders are in arrears, for example, and orders that have not yet been placed can be identified from within the application. The project planning tool facilitates material requirements planning and helps the respective assembly purchasers in particular to convert existing requirements in the company into specific material orders in good time. Both applications are made available in a separate system landscape so that basic SAP upgrades can be carried out easily at any time.
Established corporate culture through transparent cooperation
The consistent use of SAP in conjunction with the innovative add-ons has significantly increased transparency within the company: Employees are now able to recognize early on when problems occur in the ordering process and take targeted countermeasures - this is an important point for plant construction, as it prevents important parts from being missing on the construction site and the planned commissioning not being met on schedule. Thanks to the clear cockpit, all employees from the design department to the dispatch department can now store project-specific data in a central system, so that valuable company knowledge is no longer just in the heads of the employees, but is available to everyone in the system.
"The switch to the new software solution also supports a change in our corporate culture," adds Annegret Dobelmann. "The close communication between departments, which has always characterized Loesche, is now supported and expanded by an integrative system. The necessity of this change was not clear to all employees from the outset. Familiar communication structures and work processes have changed - this is not always easy. But in the end it pays off because our processes have become much more transparent and efficient. The employees quickly noticed that too."
Due to the complexity of the IT project, there were initially minor performance problems after going live, but these were resolved quickly and unbureaucratically by Milliarum's support team. In the event of any teething troubles, the follow-up support phase was planned from the outset for a longer period, namely until the end of the first quarter of 2012. But Loesche intends to maintain its collaboration with Milliarum beyond this. In addition to extending the SAP-based solutions to the Group's subsidiaries, supplementary tools are also planned in other business areas, including a complete mapping of the concurrent calculation for major projects in SAP.